The Ultimate Guide to Plastic Molding Services: Revolutionizing Manufacturing
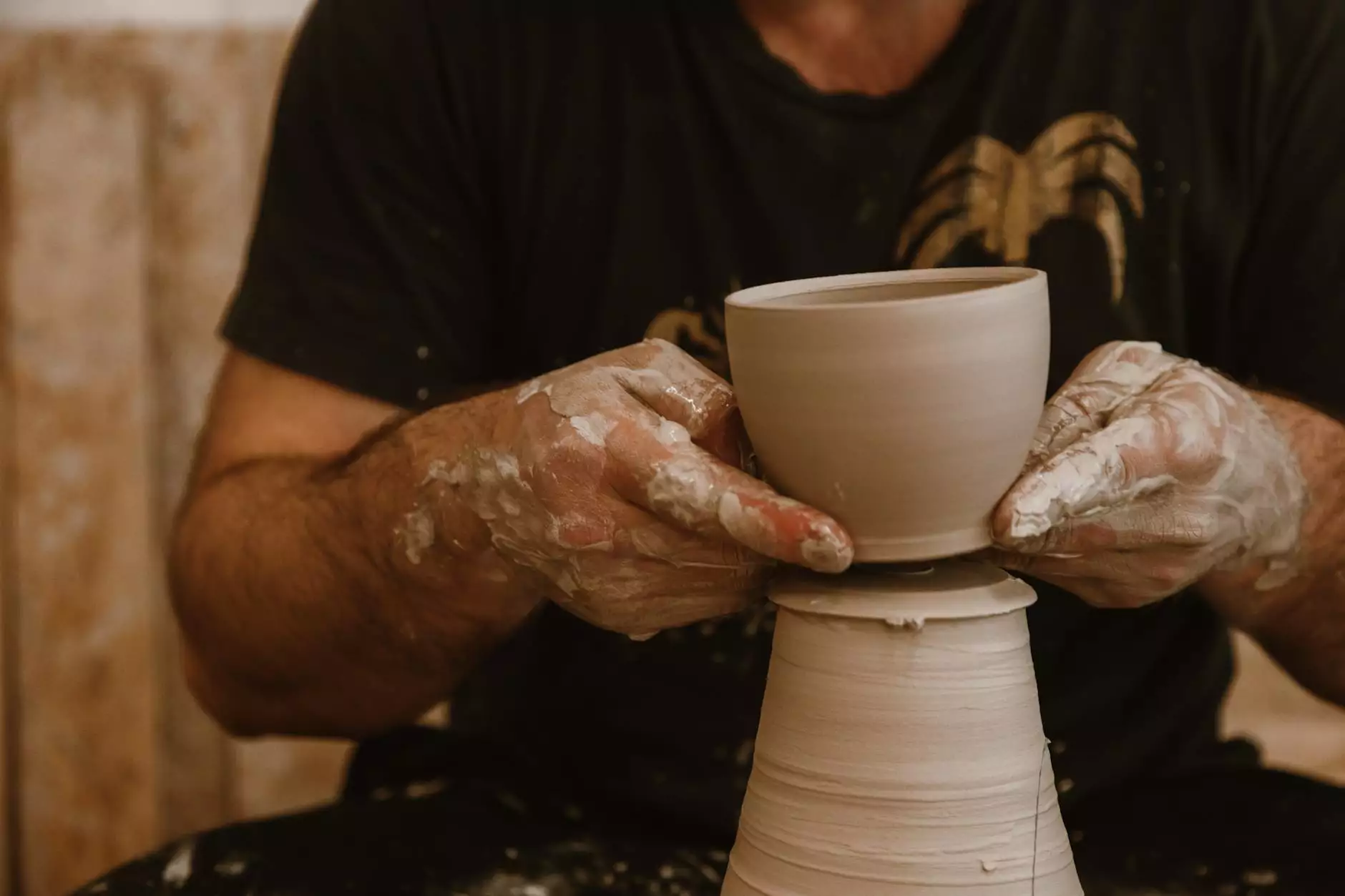
In today’s competitive manufacturing landscape, plastic molding services have emerged as a crucial technique in the production of versatile and impactful parts. Whether it's for automotive, medical, or consumer goods, understanding the intricacies of plastic molding can significantly benefit your business. This article delves deep into the world of plastic molding services, exploring types, benefits, applications, and much more.
What are Plastic Molding Services?
Plastic molding services refer to a variety of processes that create plastic products through the molding method. This technique involves heating plastic until it liquefies and then injecting or pouring it into a pre-designed mold. Once cooled, the mold is removed to reveal the finished product. This method is widely employed across different sectors, thanks to its adaptability and efficiency.
The Different Types of Plastic Molding Services
There are several methods within the realm of plastic molding services, each with its unique advantages and specific applications. Here, we will explore the most common types:
1. Injection Molding
Injection molding is one of the most popular methods of plastic production. It involves injecting molten plastic into a precisely designed mold. This technique is highly efficient for mass production and is ideal for creating intricate designs with high levels of consistency and precision.
2. Blow Molding
Blow molding is primarily used for creating hollow plastic objects, such as bottles and containers. The process involves inflating hot plastic within a mold, forming a seamless hollow structure. This method is very effective for producing large quantities of uniform items.
3. Compression Molding
Compression molding is a technique where a preheated polymer is placed into an open, heated mold cavity. The mold is then closed, and heat and pressure cause the material to conform to the shape of the mold. This method is especially useful for thermosetting plastics and is often employed in automotive and aerospace applications.
4. Rotational Molding
Rotational molding uses a rotating mold to create seamless hollow parts. The process is known for producing large, durable items, like containers and playground equipment. It allows for uniform thickness and is highly cost-effective when producing large components.
Benefits of Utilizing Plastic Molding Services
Investing in plastic molding services can greatly enhance your business. Here are some compelling benefits:
- Cost-Effective Production: Once the initial mold is created, producing each additional unit becomes significantly cheaper.
- High Efficiency: Plastic molding processes are capable of producing large volumes of product in a short period.
- Design Flexibility: Molding can accommodate complex designs, enabling intricate components that would be challenging to achieve through other methods.
- Material Variety: Various types of plastics can be molded, allowing for the creation of products tailored to specific requirements.
- Reduced Waste: The precision of molding processes leads to less waste material compared to traditional manufacturing techniques.
Applications of Plastic Molding Services
The versatility of plastic molding services allows for a wide array of applications across numerous industries:
1. Aerospace
The aerospace industry utilizes plastic molding services to create lightweight and durable parts for aircraft, which are crucial for enhancing fuel efficiency and improving overall performance.
2. Automotive
In the automotive sector, plastic molding is used to manufacture parts such as dashboards, bumpers, and interior components, drastically reducing the weight of vehicles while maintaining structural integrity.
3. Medical Devices
The precision offered by plastic molding services is essential in the production of medical devices, ensuring that products meet stringent regulatory standards for quality and safety.
4. Consumer Products
From toys to household items, plastic molding services create countless consumer goods. The process allows designers to innovate consistently while producing cost-effective items.
5. Industrial Components
Many industrial applications leverage plastic molding for the manufacturing of parts that require durability and resistance to chemicals, such as fittings and housings.